FORGE
TOOLMAN has over 67 years of experience in forging high-quality steel grades. Our advanced techniques enable us to produce forgings of various sizes and specifications including Rounds, Squares, Flats, Blanks and Upset Forging.
Forging : Ingots are processed to become round, square or flat bars in the 7- pneumatic forging hammers or 1250 ton Hydraulic Forging Press so that it can meet different demands in the market.
Rolling: The forged billets are processed by 3-high roughing mill and hydraulic CNC precision rolling mill to round bars. The equipment is characterised by fast roll replacement, high precision, and high production flexibility to meet customer needs.
-
Main equipment:
- 7 pneumatic Forging Hammers
- 1250-ton hydraulic Forging Press
- 3-high roughing mill
- Hydraulic CNC precision Rolling Mill
Open Die Steel Forge
1250 tonne Open Die Hydraulic Forging PressCapable of complex forgings up to 10 tonnes.
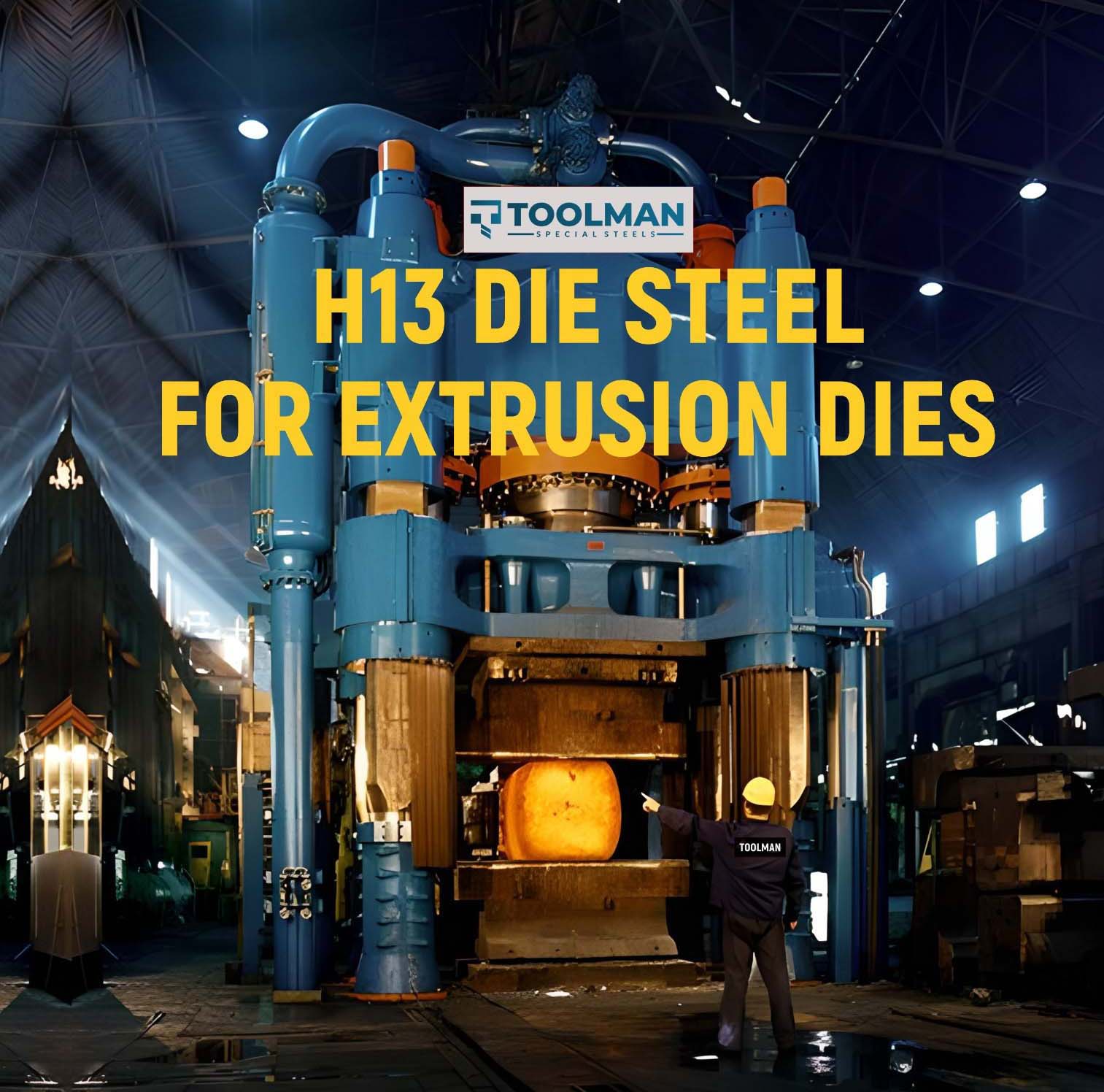
Manufacturing Range
Products | Diameter (mm) |
---|---|
Hot Rolled bar | 8 - 65 |
Forged and Turned bars | 65.2 - 500 |
Forged Square Bars | 50 - 500 |
Flats
THICKNESS | WIDTH |
---|---|
6.00 mm - 410.00 mm | 20.00 mm - 700.00 mm |
Manipulator
Fully integrated manipulators and turning gear are used for rotating during forging.
Cranes
Overhead cranes up to 25 Tons.
Forge Furnaces
Large gas fuelled re-heat furnaces are used for heating the materials to temperature prior to forging, usually around 1,250°C. Electrical overhead cranes, with lift attachments, are used to transport ingots directly from the re-heat furnaces to the press to avoid a reduction in temperature.
The forging of large ingots requires multiple forging stages and intermediate re-heating to achieve final size.