Toolman Special Steels is proud to produce and offer H11 steel, a versatile hot work tool steel known for its excellent toughness, high-temperature strength, and resistance to heat and fatigue. It is widely used in industries requiring high wear resistance and the ability to maintain hardness at elevated temperatures. Its uniform spheroidizing microstructure and great cleanliness make it a top choice for demanding applications. No matter your industry, whether it's automotive, aerospace, or general engineering, H11 steel offers exceptional performance and reliability, making it an excellent choice for your toughest applications.
Steel Properties
-
Hot work tool steel.
-
Deep hardening response.
-
High hot tensile strength.
-
Good combination of toughness, hardness and wear resistance.
-
Good thermal conductivity and resistance to softening and to cracking.
Chemical Composition
Standard | AISI (UNS) | C (%) | Si (%) | Mn (%) | P (≤ %) | S (≤ %) | Cr (%) | Mo (%) | V (%) | Ni + Cu |
---|---|---|---|---|---|---|---|---|---|---|
ASTM A681 | H11, / DIN 1.2343 /, AISI H11 / T20813 | 0.33-0.43 | 0.8-1.25 | 0.2-0.6 | ≤0.03 | ≤0.03 | 4.75-5.5 | 1.1-1.6 | 0.3-0.6 | ≤0.75 |
Mechanical Properties
ITEMS | Value |
---|---|
Annealed Hardness | Max. 235 HBW |
Hardness After Quenching | Min. 53 HRC |
Tensile strength | 1792 MPa |
Yield Strength (MPa) | 1,200 - 1,550 |
Yield Strength | 1482 MPa |
Elongation | 8% |
Impact Toughness | 13.6-33.9 J/cm2 |
Physical Properties
Property | Value |
---|---|
Density (g/cm³) | 7.8 g/cm³ |
Modulus of Elasticity (GPa) | 215 |
Modulus of Elasticity
Condition | Value |
---|---|
At 500°C | 190-210 GPa |
At 600°C | 165 GPa |
Thermal Properties
Temperature (℃) | Thermal Expansion Coefficient (10^-6/℃) |
---|---|
500 | 12.9 |
600 | 13 |
Thermal Conductivity
Temperature (℃) | W/m•K |
---|---|
500 | 28.3 |
600 | 29.3 |
HEAT TREATMENT AND PROCESSES
Preheating
Preheat the H11, / DIN 1.2343 /, AISI H11 / steel component slowly and uniformly to the desired austenitizing temperature. This helps to reduce the risk of cracking during subsequent heating.
Austenitizing
Heat the preheated H11, / DIN 1.2343 /, AISI H11 / steel to the austenitizing temperature range of approximately 1010-1095°C (1850-2000°F), depending on the specific requirements and the desired properties. Hold the steel at this temperature for sufficient time to ensure complete transformation to austenite
Quenching
Quench the austenitized H11, / DIN 1.2343 /, AISI H11 / steel rapidly in a suitable quenching medium. Common quenching media for H11 steel include oil, air, and specialized quenching baths. Quenching rates and media selection should be chosen carefully to achieve the desired hardness and minimize distortion or cracking.
Tempering
After quenching, immediately temper the hardened H11, / DIN 1.2343 /, AISI H11 / steel to relieve internal stresses and achieve the desired balance of hardness and toughness. Temperatures typically range from 540-650°C (1000-1200°F), depending on the specific application requirements. Hold the steel at the tempering temperature for the recommended duration, often a minimum of two hours, and allow it to cool in still air.
Multiple Tempering Cycles
Depending on the application and desired properties, multiple tempering cycles may be necessary. This process involves reheating the tempered steel to the tempering temperature and holding it for a specified time before cooling again.
Martempering bath or fluidised bed at approx. 180 - 220°C then cool in air Warm oil
Stress Relief Annealing
If necessary, stress relief annealing can be performed at temperatures ranging from 600-650°C (1110-1200°F) for a minimum of four hours to reduce internal stresses and improve dimensional stability.
Controlled Cooling
Throughout the heat treatment process, maintain control over the cooling rate to minimize the risk of distortion, cracking, or excessive residual stresses in the H11 steel component.
Post-Heat Treatment Inspection
After heat treatment, conduct thorough inspections of the H11, / DIN 1.2343 /, AISI H11 / steel component to ensure that the desired mechanical properties, such as hardness, toughness, and dimensional accuracy, have been achieved.
It's important to note that specific heat treatment parameters may vary depending on factors such as the size and shape of the H11 steel component, the desired mechanical properties, and the equipment available.
Heat treatment
Temperature | Duration | Cooling | |
---|---|---|---|
Soft annealing | 800 - 860 °C | 2 - 5 h | furnace |
Stress-relief annealing | 600 - 650 °C | min. 4 h | furnace |
Hardening | 1020 - 1060 °C | Group II | oil, air, WB 500 °C |
Tempering | 530 - 700 °C | min. 2 h | still air |
Tempering °C | HRC |
---|---|
100 | 52 |
200 | 52 |
300 | 52 |
400 | 52 |
500 | 54 |
550 | 53 |
600 | 48 |
650 | 37 |
700 | 31 |
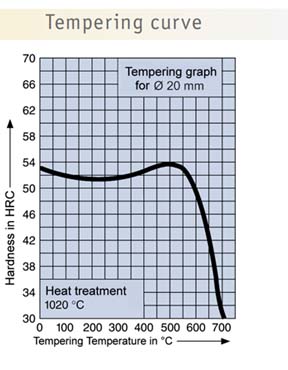
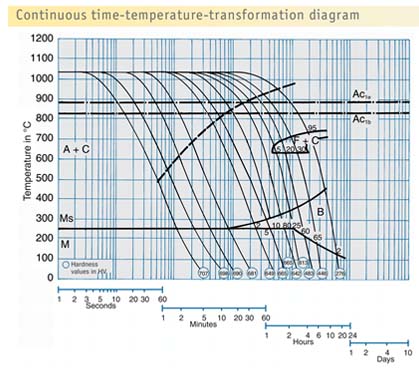
Applications
-
Die Casting Dies :H11, / DIN 1.2343 /, AISI H11 / is suitable for die casting dies for aluminum, magnesium, and zinc alloys due to its high hot strength, thermal fatigue resistance, and good thermal conductivity.
-
Forging : In the forging industry, H11, / DIN 1.2343 /, AISI H11 / finds application in forging dies and tools where high toughness and resistance to thermal fatigue are required
-
Extrusion :The steel is utilized in extrusion dies for aluminum and brass alloys, providing good thermal conductivity and resistance to thermal cracking.
-
Plastic Molding :H11, / DIN 1.2343 /, AISI H11 / steel is employed in injection mold tooling and extrusion dies in plastic molding applications due to its high hot hardness and resistance to thermal fatigue.
-
Bridge kind tools, liner holders, extrusion tooling, Hot work punches, Hot gripper dies, Aircraft landing gear and shrink work chucks, Tools for hot forging of light metal,Pressure die casting tools. Dies, mandrels, punchers, knives, moulds.
-
Shear Blades : Utilized in the production of blades that cut through metals, maintaining sharpness and integrity over extended use.
Quality Assurance
Our H11 steel undergoes rigorous testing and quality control to meet international standards, ensuring consistent performance and reliability. Certificates and test reports are available upon request. Feel free to reach out to us for more information on our H11 steel products or to discuss your specific requirements. We're dedicated to providing top-quality steel solutions that meet your needs and exceed your expectations.
Manufacturing Range
Products | Diameter (mm) |
---|---|
Hot Rolled bar | 8 - 65 |
Forged and Turned bars | 65.2 - 500 |
Forged Square Bars | 50 - 500 |
Flats
THICKNESS | WIDTH |
---|---|
6.00 mm - 410.00 mm | 20.00 mm - 700.00 mm |