Toolman Special Steels is proud to produce and offer H13, / DIN 1.2344 /, AISI H13 steel, a versatile and widely used chromium-molybdenum hot work steel. Known for its exceptional combination of high toughness and resistance to thermal fatigue, our H13, / DIN 1.2344 /, AISI H13 steel meets the highest industry standards for quality and performance. It will give an extra margin of safety in tools subject to hammer blows and those tools containing deep recesses and sharp corners. While H13, / DIN 1.2344 /, AISI H13 is designed primarily as a hot work tool steel, it has solved many cold work applications where extra toughness was required at the sacrifice of some wear resistance. Below, you'll find comprehensive details about our H13, / DIN 1.2344 /, AISI H13 steel, its applications, and its technical specifications.
Steel Properties
-
Thermal Stability : Retains mechanical properties at elevated temperatures.
-
Toughness : High resistance to cracking and impact, enhancing tool life.
-
Versatility : Suitable for various hot work applications, providing flexibility in manufacturing processes.
-
Wear Resistance : Prolongs the lifespan of tools and dies, reducing downtime and maintenance costs.
-
Machinability : Offers good machinability in the annealed condition, facilitating easier fabrication.
Chemical Composition
Standard | AISI (UNS) | C (%) | Si (%) | Mn (%) | P (≤ %) | S (≤ %) | Cr (%) | Mo (%) | V (%) |
---|---|---|---|---|---|---|---|---|---|
ASTM A681 | H13, / DIN 1.2344 /, AISI H13 (T20813) | 0.32 - 0.45 | 0.80 - 1.25 | 0.20 - 0.60 | 0.030 | 0.030 | 4.75 - 5.50 | 1.10 - 1.75 | 0.80 - 1.20 |
Mechanical Properties
ITEMS | Value |
---|---|
Hardness (HBW) | 235 MAX (ANNEALED) |
Hardness After Quenching (HRC) | 52 MIN. (ANNEALED) |
Tensile Strength (MPa) | 1,450 - 1,950 |
Yield Strength (MPa) | 1,200 - 1,550 |
Elongation at Break | 10 - 15 % |
Impact Toughness (J at 20°C) | 20 - 30 |
Physical Properties
Property | Value |
---|---|
Density (g/cm³) | 7.80 |
Modulus of Elasticity (GPa) | 215 |
Thermal Properties
Temperature (℃) | Thermal Expansion Coefficient (10^-6/℃) |
---|---|
300 | 12.2 |
400 | 12.5 |
500 | 12.9 |
600 | 13 |
Thermal Conductivity
Temperature (℃) | W/m•K |
---|---|
20 | 25 |
500 | 28.3 |
600 | 29.3 |
HEAT TREATMENT AND PROCESSES
Soft Annealing
Protect the steel and heat through to 750 - 800°C. Then cool in the furnace at 10 - 20°C per hour to 600°C, then freely in air.
Stress Relieving
After rough machining, the tool should be heated through to 650°C, holding time 2 hours. Cool slowly to 500°C, then freely in air.
Hardening
Preheating temperature: 600 - 850°C, normally in two preheating steps.
Austenitising temperature: 1020 - 1050°C, normally 1020 - 1030°C.
Protect the tool against decarburisation and oxidation during hardening
Quenching Media
High-speed gas/circulating atmosphere
High-speed gas with sufficient positive pressure quenching in vacuum furnace. Interrupted quench is recommended for distortion control, or when quench cracking is a concern.
Martempering bath or fluidised bed at 450 - 550°C, then cool in air
Soft Annealing
Protect the steel and heat through to 750 - 800°C. Then cool in the furnace at 10 - 20°C per hour to 600°C, then freely in air.
Martempering bath or fluidised bed at approx. 180 - 220°C then cool in air Warm oil
Tempering
Choose the tempering temperature according to the hardness required by reference to the tempering graph. Temper at least twice with intermediate cooling to room temperature.
Tempering °C | HRC |
---|---|
100 | 54 |
210 | 53 |
300 | 53 |
400 | 55 |
500 | 56 |
550 | 54 |
600 | 51 |
650 | 43 |
700 | 34 |
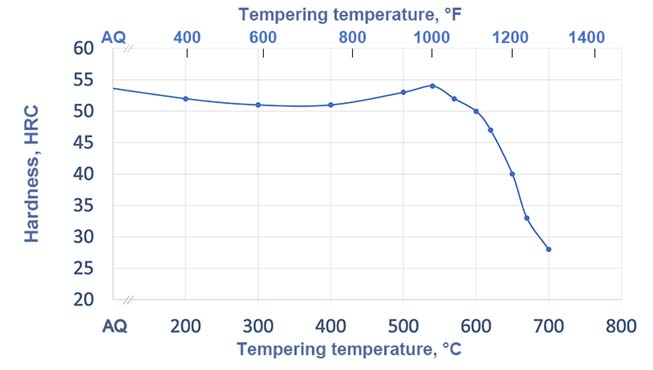
Applications
-
Die Casting Dies :Ideal for dies requiring high toughness and resistance to thermal fatigue.
-
Extrusion Tools : Used in hot extrusion processes due to its ability to withstand high temperatures and pressures.
-
Hot Forging Dies : Suitable for forging applications where high strength and resistance to impact are critical.
-
Plastic Molding : Commonly used for molds in the plastic industry, especially for producing high-quality and durable molds.
-
Punches and Dies : Employed in the manufacture of tools for cutting and shaping metals, benefiting from its wear resistance.
-
Shear Blades : Utilized in the production of blades that cut through metals, maintaining sharpness and integrity over extended use.
-
Bulldozer dies
-
Ejectors and nozzles for pressure die casting of zinc, lead and tin base alloys.
-
Used for ejector pins, tool holders and shrink fit chucks.
-
Hot cropping, billet shearing and circular shearing.
-
Metal Track Pressure Tools.
-
Inserts
-
Plungers
H13, / DIN 1.2344 /, AISI H13 ESR
H13 ESR is the most refined material. The quality of material increase the toughness, highly increase the micro- cleanness level. Extra Clean and Uniform Steel, No Macro Segregation, Extra Fine Grain, Fine Carbide Distribution.
Highly recommend the use of AISI-H13 ESR grade for Aluminium Pressure Die Casting & other component subjected to high working temperatures and high pressure strength.
H13 ESR is fully ultrasonic inspected with 100% positive results as per NDT standards.
Quality Assurance
Our H13, / DIN 1.2344 /, AISI H13 steel undergoes rigorous testing and quality control to meet international standards, ensuring consistent performance and reliability. Certificates and test reports are available upon request.
Manufacturing Range
Products | Diameter (mm) |
---|---|
Hot Rolled bar | 8 - 65 |
Forged and Turned bars | 65.2 - 500 |
Forged Square Bars | 50 - 500 |
Flats
THICKNESS | WIDTH |
---|---|
6.00 mm - 410.00 mm | 20.00 mm - 700.00 mm |